Seaway to Attend NPE Tradeshow
Orlando, Florida - May 6-10, 2024
Every three years, bold leaders, creative thinkers, and visionaries from every industry in the world gather at NPE to advance their business through innovations in plastics.
Join Seaway Plastics at NPE! Celebrating 40 Years of Engineering Excellence in 2024, we're excited to showcase our latest innovations. We will be at Booth S28137. You can find us in South Hall Level 1, to the left of the Moldmaking Zone. Claim your free expo pass using Promo Code: 590724, or click the link below.
Seaway will be offering tours of our Port Richey facility to current and potential customers during NPE. The tradeshow is just over a two hour drive from us. If you would like to schedule a tour during the week of NPE, please reach out to info@seawayplastics.com to enquire about our limited tour availability.

OUR SERVICES
INDUSTRIES
An Outstanding Commitment to Quality
CASE STUDIES
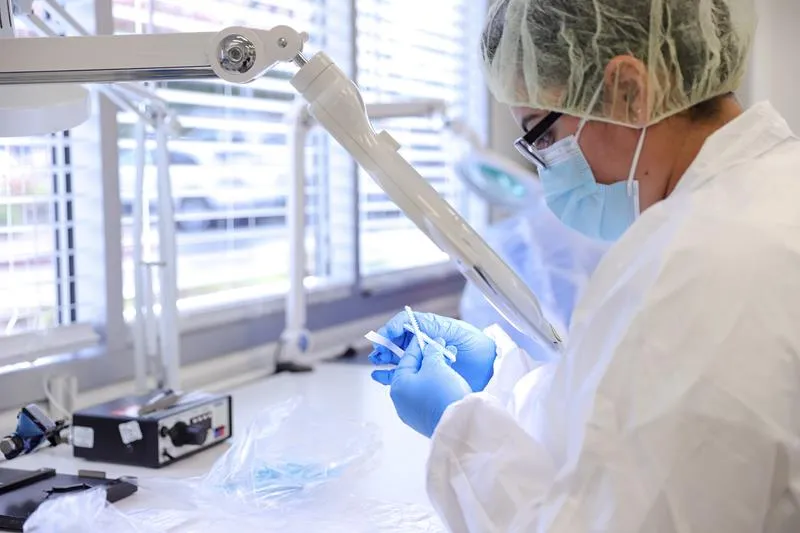
This company had been using a range of medical devices since 1949, and its 90,000+ employees and numerous science and technology breakthroughs had earned it a reputation as a pioneer…

This defense contractor has been serving the needs of defense contractors nationally and internationally since its inception in 1969. With over 4000 employees, this defense contractor has known their unique…
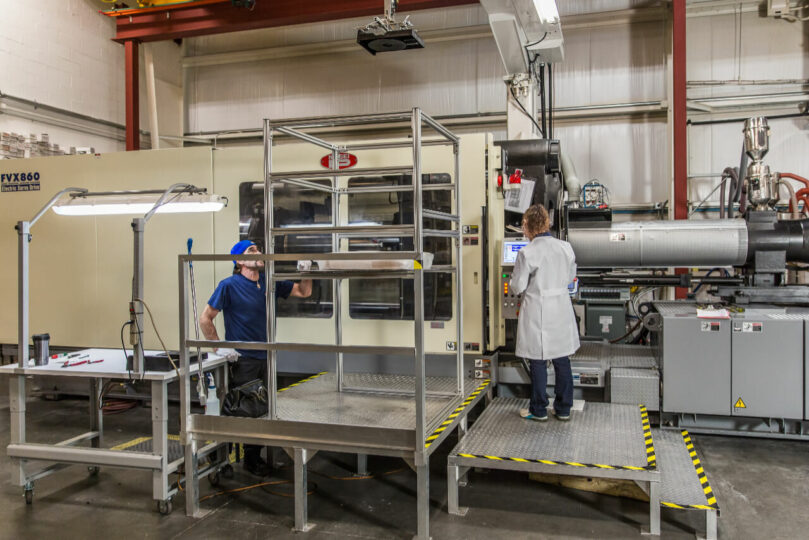
Since 1998, this aerospace company has been creating airplane parts that create a professional and safe interior. Their desire to seek new technologies and design solutions for aircraft has kept…
ABOUT SEAWAY
Seaway Plastics Engineering along with its two divisions, MME Group and Wright Engineered Plastics, is a contract manufacturer that specializes in plastic injection molding for low to higher volume projects. For more than 40 years, the company has manufactured precision parts and created complex assemblies for customers across a range of highly regulated industries, including the medical, aerospace, defense and precision industrial markets.
Qualified as an ISO 13485 certified injection molder, Seaway provides medical injection molding, cleanroom injection molding and industrial injection molding. The company offers more than 700 industrial and medical-grade thermoplastics and liquid silicone rubber (LSR) to meet the needs of any customer.
Seaway provides a full range of services to ensure end-to-end support for its customers. Full turn-key solutions include design for manufacturing (DFM), engineering, in-house tool design and build, injection molding using thermoplastics and silicone, assembly, kitting, packaging, and distribution. The company also offers an array of value-added secondary operations, such as pad printing, welding, shielding, heat staking, annealing, and much more.
Partnering with Seaway provides cost and time savings and overall efficiency for every project due to their vertical integration. This translates to reduced overall risk and faster time to market.
The company has more than 250,000 square feet of manufacturing space at five facilities across the U.S.:
All five Seaway locations are ISO 13485 certified to ensure the safe, reliable manufacturing and handling of medical devices.
With more than 35,000 square feet of ISO Class 7 & 8 cleanroom space, Seaway provides FDA-certified cleanroom injection molding and assembly. The company is equipped to manage not just the complex molding of individual parts, but any intricate mechanical and electrical assembly, validation and specialized packaging that are required to ensure the integrity of today’s specialized medical and healthcare-related products.
At Seaway, we bring an engineering mindset, world-class technologies and materials, end-to-end support, and a commitment to excellence to everything we do. Let us create customized injection molding solutions to meet your diverse and specialized manufacturing challenges.
WE’RE HERE FOR YOU
No matter what stage you’re in, we’ll guide you through the entire process.