Case Study
Industry: Medical
Our Objective
The surgical arm specified by the customer required 45 different manufactured parts and two specific challenges complicated the fabrication process. The first challenge presented is that the production of all individual plastic components for the medical device in a single location was impossible for most manufacturers. The second challenge presented was the inability of manufacturers to change the original proposed design because it would lead to problems with accuracy during surgeries.
The company expressed a desire to work with a single manufacturer to develop the necessary plastics for the medical device and reduce supply chain complexities. This specific company also had significant concerns about patent security surrounding plastics for medical devices. The company’s employees were worried about what could happen if the product and its plans changed hands too many times.
Seaway Plastics Engineering took all of these concerns seriously before starting development on the plastics for the medical device.
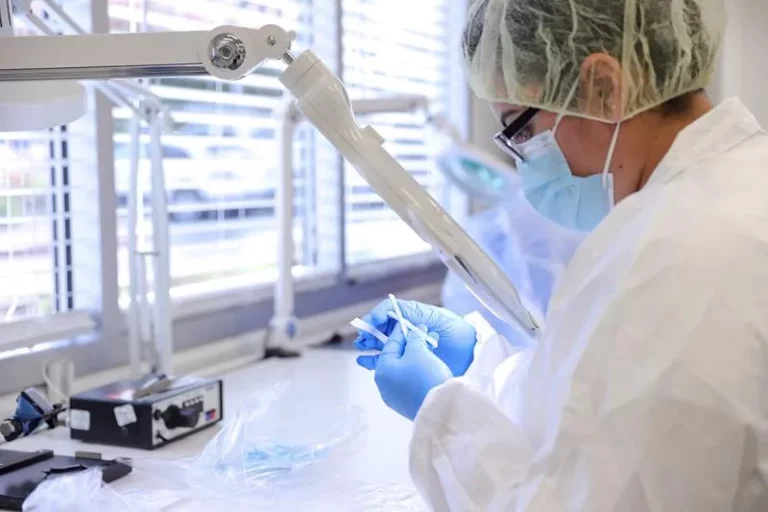

The Results
Working in tandem, Seaway Plastics Engineering and Wright Engineered Plastics were able to meet this client’s specified plastics for medical device needs by taking care of the entire process from design to product launch in their facilities. Seaway Plastics and Wright Engineered Plastics also performed all the required quality assurance and control procedures. Additionally, the customer was provided detailed reports of these procedures within days of sampling, adding even more transparency and reliability to the process.
Manufacturing the surgical arm in a singular facility enhanced security surrounding the medical device, addressing customer concerns of over-handling, while also safeguarding the integrity of the device itself. Working with a single manufacturer also improved design-for-manufacturing (DFM), tooling creation, and product testing.
This client saved over $16,000 in shipping and handling costs on top of the other expenses they would have incurred by outsourcing the manufacturing process, quality tests, and validations to another third party. This company also enjoyed more security and device integrity than it would have if it had to work with multiple manufacturers. Although these elements are hard to quantify, they represent significant value for the client and are easily applicable to any client looking to utilize plastics for medical devices.
Conclusion
With the combined experience of Seaway Plastics Engineering and Wright Engineered Plastics, the customer addressed security concerns, streamlined manufacturing, and received high-quality plastics for medical devices without compromising the accuracy or performance of the final product. Without involving third-party businesses the customer received additional cost savings on shipping, quality control testing, and validations.
Overall, this case study further supports the expertise of Seaway Plastics Engineering in developing plastics for medical devices that provide cost-savings to the customer without sacrificing quality or accuracy.
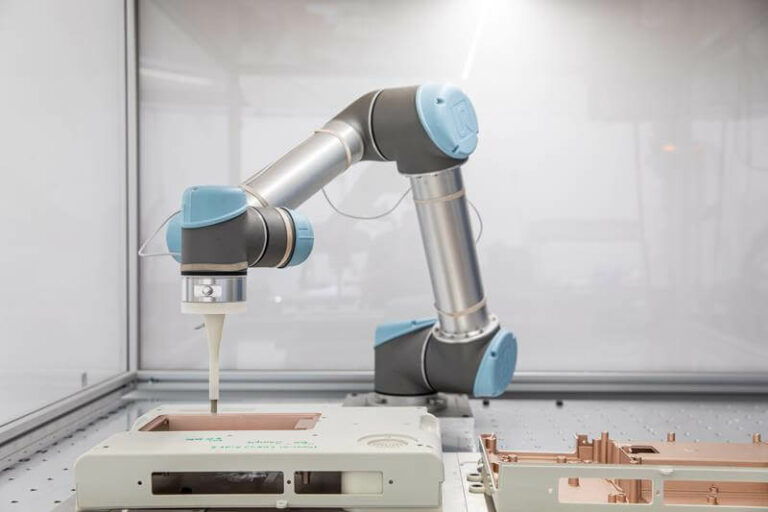