Case Study
Industry: Medical
This unique project required Wright’s expertise in clean room injection molding to provide noticeable upgrades to product quality for a spinal implant company. Wright Engineered Plastics partnered with an OEM to develop production procedures and help support the transition of their medical device into manufacturing. This leading medical technology company designs and develops advanced spinal implant technologies and assorted other biologics, with a focus on minimally invasive solutions to improve patient outcomes, expedite recovery times, and enhance surgical efficiency. Due to the implantable nature of this product, they required stringent manufacturing techniques using clean room injection molding to meet industry specifications.
Thankfully, the leading company on the project Wright Engineered Plastics maintains an ISO 13485 certification dictating quality standards for medical devices, making them an ideal choice for this project. Their industry knowledge allowed them to deliver impressive quality enhancements with clean room injection molding techniques over previous machining methods with limited product fallout. This specific spinal implant company also makes products that include spinal fusion devices, metal-free fixation systems, and advanced access systems. They are committed to enhancing patient care through innovation and philanthropy, supporting various health charities through their unique programs. The details regarding this specific project outline Wright’s advanced clean room injection molding expertise for medical applications, the impressive results, and the numerous benefits afforded to this spinal implant company after switching manufacturing processes.
Our Objective
The specific objectives of this clean room injection molding project are to limit product fallout and provide a more precise product at lower costs and faster turnaround times. Wright Engineered Plastics partnered with an OEM to establish production procedures and facilitate the transition of their medical device into manufacturing by following stringent standards dictated by our ISO 13485 certification. This included molding the components in a Class 8 clean room and assembling them in a Class 7 clean room. When there were financial constraints for the initial company leading the project, a Spinal Implant Company acquired the project and continued collaborating with Wright while focusing on optimizing production and scaling operations.
A crucial objective of this clean room injection molding project was to address the quantity limitations of the existing machining techniques used to fabricate these products for the Spinal Implant Company. Wright took on the responsibility of injection molding certain key components and freed up time for the customer to focus on the manufacturing of additional components for the final spinal implant product. Through this collaboration, Wright increased the production capacity from 25 units a month to over 200 units a month, a 700% increase!
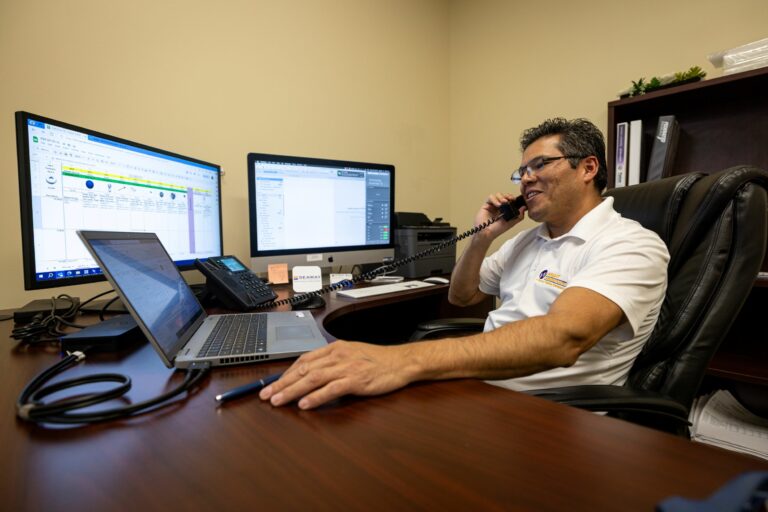
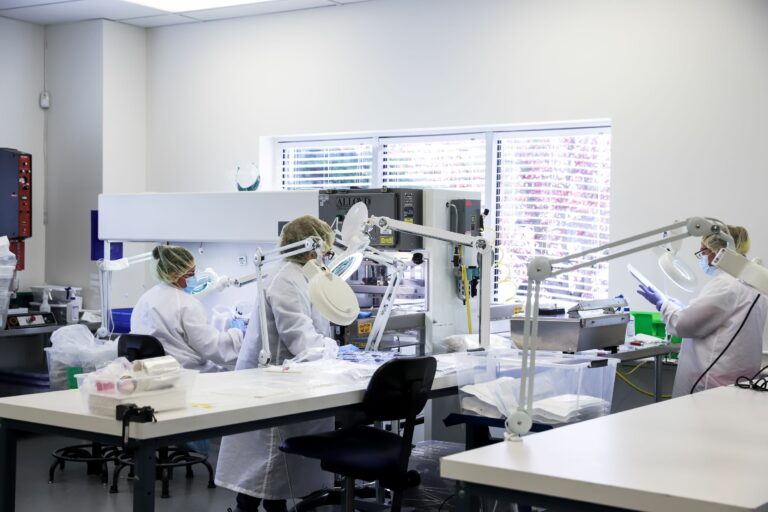
The Results
Initially, Wright worked with the OEM to develop procedures and construct a new cleanroom, enabling successful market entry. Transitioning to the Spinal Implant Company, Wright streamlined production processes, collaborated with engineers, and developed fixtures to enhance efficiency. Scaling from low to mid-volume production, Wright’s expertise facilitated the transition, enabling the production from tens to hundreds to thousands of units.
Through this collaborative process, Wright offered design suggestions for five separate components that were recently machined but could now be manufactured using clean room injection molding. Wright offered design for manufacturability improvements, managed the entire supply chain, provided a bill of materials, and performed the final cleaning and packaging operations for this product. These design improvements helped to eliminate previous failures and reduced the lead times and costs associated with previous machining methods.
Conclusion
Wright’s partnership with both companies resulted in a significant reduction in line fallout from 20% to 2%, demonstrating improved efficiency and quality control and dramatically increased component output through fast turnaround clean room injection molding techniques. Transitioning production of these integral medical components to plastic injection molding from machined parts expedited time-to-market, reduced stress points, and contributed to cost savings. Beyond production optimization, Wright’s involvement in troubleshooting and packaging refinement ensured correct device functionality and efficient packaging processes, establishing a lasting partnership built on trust and proven results. Many medical companies looking to expedite production, reduce costs, and provide higher-quality components to patients should consider utilizing Wright’s expertise in clean room injection molding. If you are interested in learning more about our process, please contact a member of our team today for more information or a quote.
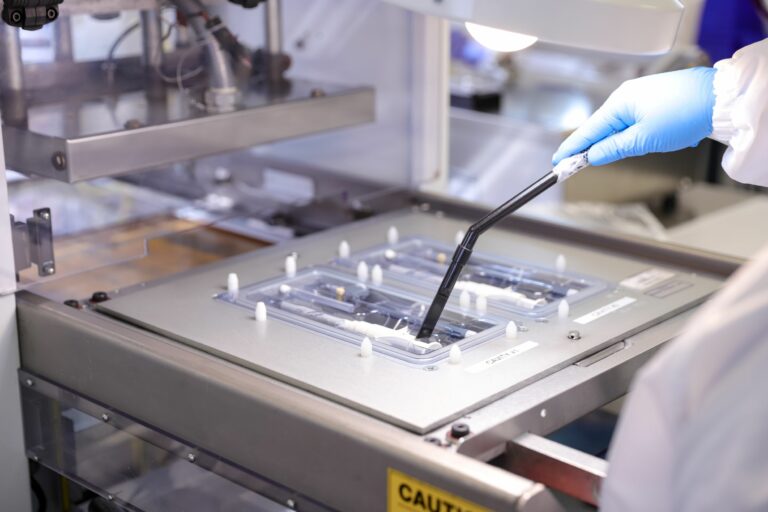