Case Study
Industry: Medical
A global healthcare company, recognized for its innovation in diagnostics and medical devices, approached Wright Engineered Plastics, a Seaway Plastics company, to address production challenges in one of their essential products. This company, a leader in developing life-changing technologies aimed at improving health and well-being, required a solution that would ensure product reliability while reducing costs.
Our Objective
The objective was to improve the production consistency of two molded halves that encapsulate a diaphragm, creating a hermetically sealed, waterproof unit. Wright Engineered Plastics originally developed this product in collaboration with the customer’s engineering team, coining the term “centerless molding” in the process. Before Wright took on the project, a similar product was manufactured using a glued assembly method, which often required leak testing. The challenge was to enhance yield, reduce waste, and lower production costs while ensuring the high reliability of the final product.
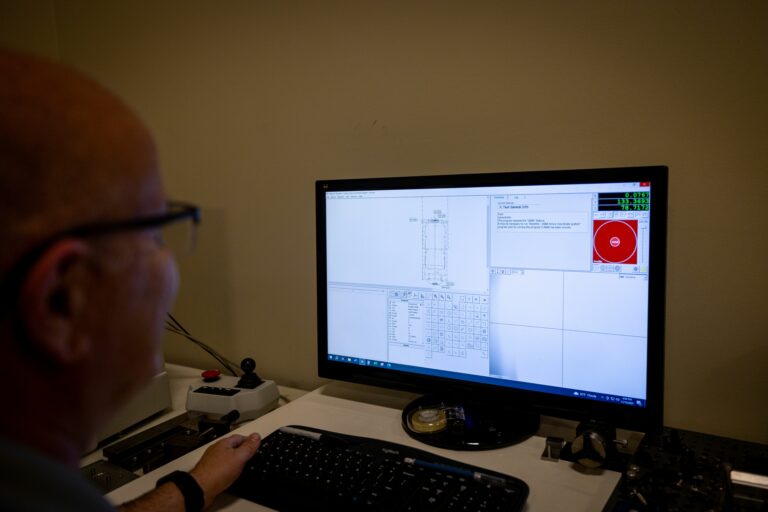
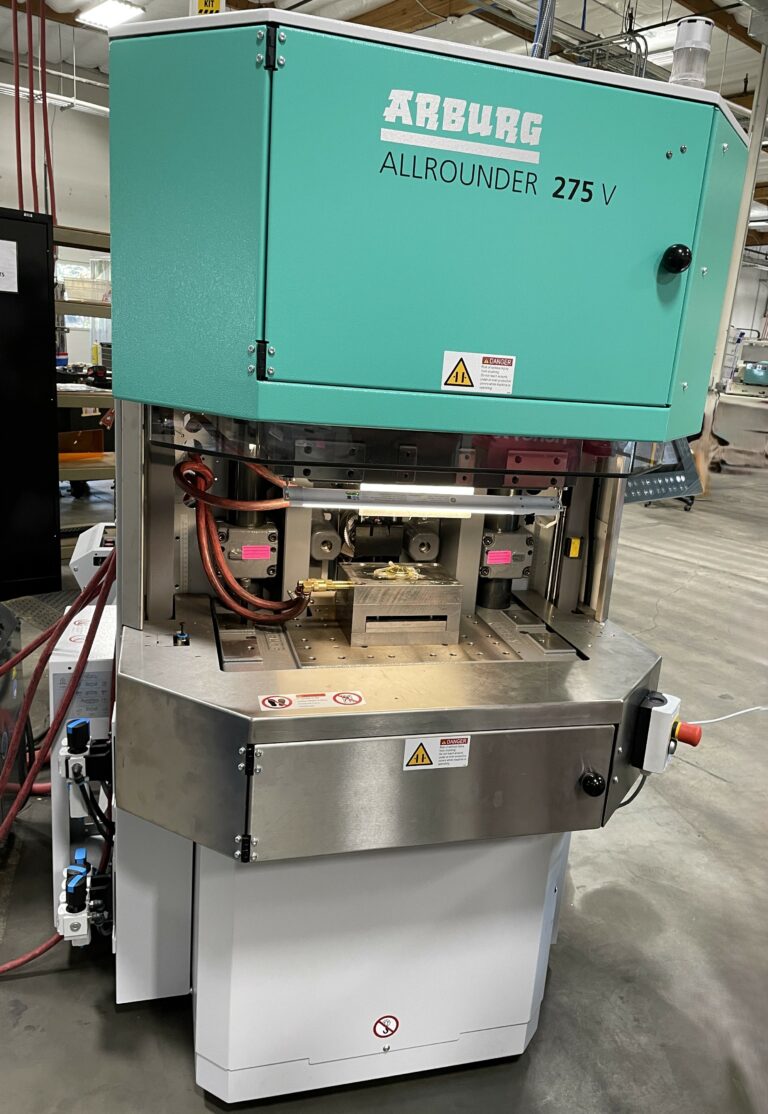
The Results
Initially, the production process using an older vertical injection molding press resulted in a low yield, with only 30%-40% of parts meeting the customer’s stringent quality standards. The customer was aware of these challenges, and Wright was determined to improve the process. By investing in a new vertical injection molding press, Wright was able to significantly enhance the molding process’s precision and consistency. The success rate of molded products increased to 83%, more than doubling the yield. This improvement not only reduced waste but also lowered the overall production costs.
To ensure quality, Wright implemented stringent QA standards. For the first shot molding, standard height and radii measurements were taken. After overmolding, each unit was verified using a vision system program to check the mounting holes. Additionally, a volume verification test was conducted for each pump, where the pump was filled with water and its output was measured to within ±0.05 ml. This rigorous testing process ensured that each product met the necessary waterproofing and functionality requirements.
Conclusion
The implementation of advanced vertical injection molding technology at Wright Engineered Plastics led to substantial improvements in product yield and consistency. By upgrading their equipment and refining the molding process, Wright was able to meet the customer’s needs more effectively, reducing costs and enhancing product reliability. This success has strengthened the partnership, resulting in additional projects from the customer and further demonstrating Wright’s commitment to delivering high-quality, cost-effective solutions.
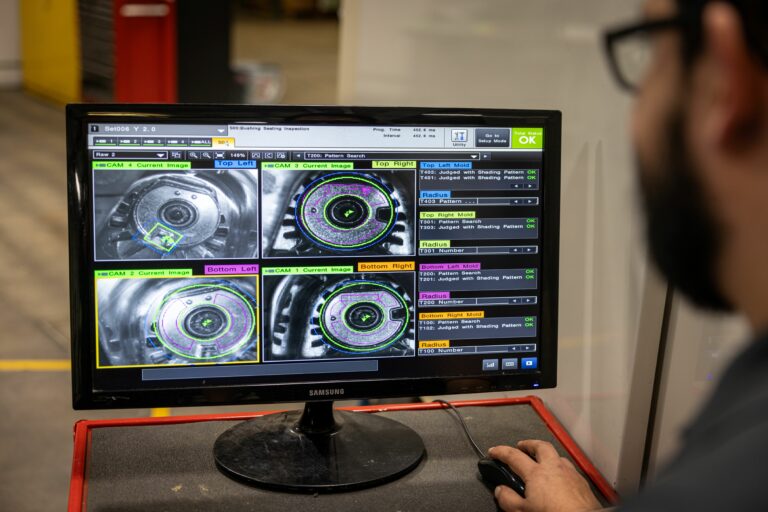